MUFFLE FURNACE
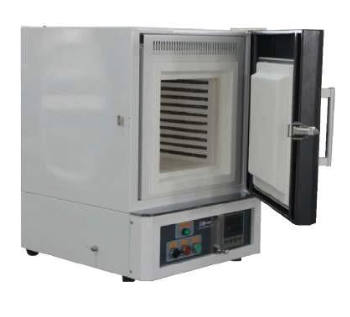
Features
♦Maximum operating temperature range upto180o•c.
♦Dimensions from 1 upto 200 litres.
♦Rugged and durable Construction.
♦Outer cosing is mode up thick mild steel with duly powder coated or thick buffed stainless steel, gives long service life with extremely resistant.
♦Multi-layer insulation with vacuum formed ceramic fibre or refractory bricks with low thermal mass.
♦Parallel guided swing aside door design.
♦Furnace design with powerful heating elements. i.e.FeCrAI, SiC and MoSi2 in both sides providing fast heating rate.Fast heat up and cool down roles.
♦Temperature uniformity+/-5°C.
♦Temperature control with PIO controllers.
♦Power control with solid state relays or Thyristor units for very precise temperature Control,wear-free and noiseless.
♦High mechanical durability,short heating cycle and low power consumption.
Options
♦ Over Temperature/Over Current limiter
♦ Touchscreen temperature controller
♦ Port for additional thermo couple.
♦ Process observation window.
♦ Chimney for forced air extraction.
♦ Additional ceramic/SiC bottom plate.
♦ Buzzer, Digital timer, Emergency shut down.
♦ Data Recorder .
♦ RS232/RS485/USB interface .
♦ Calibration of temperature measurement systems.
♦ Gas purging facility Table for supporting the systems.
♦ Data Acquisition System (DAS) through software.
♦ UPS Systems.
♦ Customization as per user requirement.
Applications
Muffle Furnace is designed for R & D labs, Educational institutions, Medicine and Industry,
Chemical Industries,Plastic Industry, Moulding Industry,Glass Industry,Rubber Industry,
Ceramics Industry ,Biomedical Industry,Point Industry,Textile Materials,
Pharma Industry, Dental Lobs ,Thermal Process Technology ,Advanced Materials for following applications,Testing,
Analysing, Ashing, Drying, Sintering, Annealing, Melting, Tempering, Hardening, Dental Porcelain and Crystallising etc.
SPLIT TUBE FURNACE
Features
♦Maximum operating temperature range upto 1500°C. .
♦ Available in Horizontal operation, Vertical operation, universal operation.
♦Furnace split into two halves.
♦ Split design allows to insert tubes with large flanges.
♦ Accelerate cooling of furnace and tube by opening hinges casing.
♦ Compact design for minimum space requirement.
♦ Rugged and durable Construction.
♦ Outer casing is made up thick mild steel with duly powder coated or thick buffed stainless steel,
gives long service life with extremely resistant.
♦Multi-layer insulation with vacuum formed ceramic fibre or refractory bricks with low thermal moss.
♦Alumina/Quartz/Metal tube with two fibre plugs included
♦ Inner diameter of the tube from 20mm to 150mm.
♦Heated Length from 100mm to 1000mm.
♦Furnace design with powerful heating elements i.e . FeCrAI, and SiC in all side s of the work tube providing fast heating rate.
♦ Fast heat up and cool down rates.
♦Temperature uniformity + / - 5°C.
♦Temperature control with PID controllers.
♦Power control with solid state relays or Thyristor units for very precise temperature Control, wear-free and noiseless.
♦ High mechanical durability, short heating cycle and low power consumption.
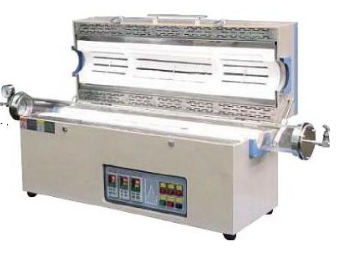
Options
♦ Multi-zone temperature control.
♦ Touchscreen temperature controller.
♦ Over Temperature Limiter.
♦ Vacuum pump with fittings.
♦ Gas and Vacuum Compatible Flanges, Water cooled flanges with chiller.
♦ Door flanges with hinges.
♦ Gas mixing system
♦ Digital/Analog flow meters.
♦ Port for additional thermo couple on the flange.
♦ Process observation window on flange.
.♦ Buzzer, Digital timer, Emergency shut down.
♦ Data Recorder.
♦ RS232/ RS485/ USB interface.
♦ Calibration of temperature measurement systems.
♦ Table/Stand for supporting the systems.
♦ Data Acquisition System (DAS) through software.
♦ UPS Systems.
♦ Customisation as per user requirement.
♦ Caster wheels with brakes.
♦ Door safety switch.
Applications
Split Tube Furnace is designed for R&D labs, Educational institutions, Medicine and Industry,
Chemical Industries, Ceramics Industry, Biomedical Industry, Pharma Industry,
Thermal Process Technology, Advanced Materials for following applications -
Purification, Cooling, Drying, Hardening or Ageing of samples, Annealing, Brazing,
Calcination, Degassing, Sintering, Tempering, Thermocouple calibration, Testing of fuel cells,
Catalyst research, Inorganic and Organic purification, Coating etc.
DENTAL FURNACE
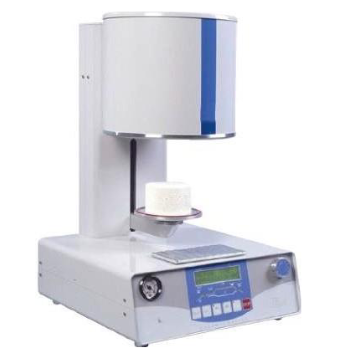
Features
♦ Maximum operating temperature range up to 1600°C.
♦ Dimensions from 1 up to 64 litres.
♦ Compact design for minimum space requirement.
♦ Rugged and durable construction.
♦ Outer cosing is mode up thick mild steel with duly powder coated or thick buffed stainless steel, gives long service life with extremely resistant.
♦ Prepared to carry heavy charge weight.
♦ High mechanical durability, short heating cycle and low power consumption.
♦ Multi layer insulation with vacuum formed ceramic fibre or refractory bricks with low thermal moss.
♦ Hot raising by hydraulic.
♦ Sintering troys are filled with o bed of zirconium supports beads. These trays are design to fit exactly on furnace hearth.
♦ The bed of zirconio beads allows sintering process with low friction and result in distortion-free frameworks.
♦ Exhaust air vent in roof.
♦ Precise, Motorised operation of the hearth with button.
♦ Reliable vibration free bottom lifting with electro-mechanical movement.
♦ Fast heat up and cool down rates.
♦ In contrasts to SiC/MoSi2 heating elements, these ore free from any chemical interaction with zirconium oxide.
♦ Due to all round furnace chamber heating, high process stability and excellent temperature uniformity up lo +/- 5°C Temperature control with PIO controllers.
♦Power control with solid state relays or Thyristor units for very precise temperature Control, wear-free and noiseless.
Options
♦ Touch screen temperature controller.
♦ Over Temperature/ Over Current limiter.
♦ Port for additional thermo couple on
top or rear wall of the furnace.
♦ Buzzer, Digital timer, Emergency shut down.
♦ Data Recorder.
♦ RS232/RS485/USB interface.
♦ Calibration of temperature measurement systems.
♦ Table/Stand for supporting the systems.
♦ Data Acquisition System (DAS) through software.
♦ Spare sinter trays and support beads.
♦ UPS Systems.
♦ Customization as per user requirement.
♦ Caster wheels with brakes.
♦ Door safety switch.
Applications
Dental Furnace is designed for R&D labs, Educational institutions, Thermal process Technology,Dental Labs,and
Advanced Materials for following applications -
Drying, Hardening, Sintering, Research, Heat Treatment,Dental crowns and frameworks etc.,
ROTARY TUBE FURNACE
Features
♦ Maximum operating temperature range up to 1500°C.
♦ The rotary tube furnace allows samples to be heated and mixed simultaneously in a controlled atmosphere
Furnace split into two halves.
♦ The design of split furnace allows Work tube to be easily removed and replaced
Split design allows to insert tubes with large flanges
.
♦ Split cover enables faster cooling and easy operation
Compact design for minimum space requirement.
♦ Rugged and durable Construction.
♦ Outer cosing is mode up thick mild steel with duly powder coated or thick buffed stainless steel, gives long service life with extremely resistant.
♦ Multi-layer insulation with vacuum formed ceramic fibre or refractory bricks with low thermal mass.
♦ Working tube mode of either ceramic, quartz, or a high-temperature alloy with two fibre plugs included.
♦ Inner diameter of the tube from 20 mm lo 150 mm.
♦ Heated length from 100 mm to 1000 mm.
♦ Furnace design with powerful heating elements i.e., FeCrAI, and SiC in all sides of the work tube providing fast heating rote.
♦ Adjustable inclination angle up to 30°.
♦ Variable speed control system up to 20RPM.
♦ Fast heat up and cool down rates.
♦ Temperature uniformity +/- 5 °C.
♦ Temperature control with PIO controllers.
♦ Power control with solid stole relays or Thyristor units for very precise temperature Control, wear-free and noiseless.
♦ High mechanical durability, short heating cycle and low power consumption.
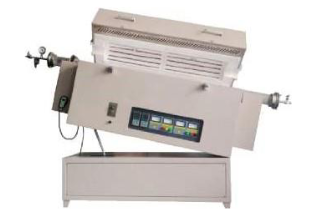
Options
♦ Multi- zone temperature control.
♦ Touchscreen temperature controller.
♦ Over Temperature/Over Current Limiter.
♦ Vacuum pump with fittings.
♦ Gas and Vacuum Compatible Flanges, Water cooled flanges with chiller
♦ Door flanges with hinges.
♦ Gas and Vacuum control accessories.
♦ Gas mixing system Digital/Analog flow meters.
♦ Port for additional thermo couple on the flange.
♦ Process observation window on flange.
♦ Buzzer, Digital timer, Emergency shutdown.
♦ Data Recorder.
♦ RS232/RS485/USB interface .
♦ Calibration of temperature measurement systems.
♦ Table/ Stand for supporting the systems.
♦ Data Acquisition System (DAS) through software.
♦ UPS Systems.
♦ Customisation as per user requirement.
♦ Caster wheels with brakes.
Applications
Rotary Tube Furnace is designed for R&D labs, Educational institutions, Medicine and Industry,
Chemical Industries, Ceramics Industry, Biomedical Industry, Pharma Industry,
Thermal Process Technology, Advanced Materials for following applications-
Purificolion,, Pyrolysis, Carburizotion, Solid state reaction, Waste remediation, Drying,
Thermal recycling,Calcination,Oxidation,Reduction.
TOP LOADING FURNACE
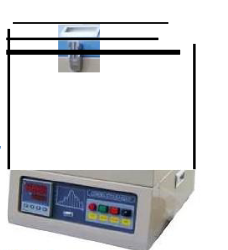
Features
♦ Maximum operating temperature range up to 1450°C.
♦ Available in various capacity, from 3 litres to 250 litres.
♦ As the name states itself, top loading fumoces ore mode vertical heating chambers;
where material or crucible is put from top.
♦ Door is fitted on top, which is lift up to open and put down to close.
♦ Usually such furnaces ore used to put crucibles; the refore, these furnaces ore also called crucible furnace.
♦ These Top loading chamber furnaces ore particularly suited for applications involving toll crucibles and
heavy components.
♦ Top cover allows better heat shielding and more uniform heating area.
♦ Top opening provides good ventilation inside the chamber and allow the furnace to fast cooling.
♦ Ideal for heavy components and provides safety in loading/ Unloading.
♦ Sturdy, locking castors for easy movement of the system.
♦ Compact design for minimum space requirement.
♦ Rugged and durable Construction.
♦ Outer cosing is mode up thick mild steel with duly powder coated or thick buffed stainless steel, gives long service life with extremely resistant.
♦ Multi-layer insulation with vacuum formed ceramic fibre or refractory bricks with low thermal mass.
♦ Furnace design with powerful heating elements i.e. FeCrAI, and SiC in all sides of the work tube providing fast heating role.
♦ Heating elements in all four walls minimise the risk of damage from,
spills and ensure good temperature uniformity.
♦ Fast heat up and cool down rates.
♦ Temperature control with PIO controllers.
♦ Power control with solid state relays or Thyristor units for very precise temperature Control, wear-free and noiseless.
♦ High mechanical durability, short heating cycle and low power consumption.
Options
♦ Over temperature/Over current limiter.
♦ Touchscreen temperature controller.
♦ Process observation window.
♦ Chimney for forced air extraction.
♦ Buzzer, Digital timer, Emergency shutdown.
♦ Data Recorder.
♦ RS232/RS485/USB interface.
♦ Calibration of temperature measurement systems.
♦ Table/Stand for supporting the systems.
♦ Data Acquisition System (DAS) through software.
♦ UPS Systems.
♦ Customization as per user requirement.
♦ Caster wheels with brakes.
♦ Door safety switch.
Applications
Top loading Furnace is designed for R&D labs,Educational institutions, Medicine and Industry,
Ceramics industry, Biomedical Industry, Glass industry Pharma industry, Thermal Process Technology,
Advanced Materials for following applications -
Drying, Hardening, Annealing, Brazing, Degassing, Sintering, Tempering, , Testing of fuel cells,
Inorganic and Organic purification, Heat treatment, Stress releoving, Component Testing, Preliminary Heating,
loosening, Normalising, Melting etc.
CVD FURNACES
Features
♦ Maximum operating temperature range up to 1200°C.
♦ The CVD furnace woncstotion consists Split Tube/Tube furnace, a precision mass flow gas control station, a high vacuum station,
and other assembling ports.
♦ The mass flow gas control station mixes multiple gases together and allows the mixed gas to flow into a fused quartz tube inside
the furnace.
♦ Processing tube is included Inner diameter of the tube from 40 mm to 150 mm with vacuum stainless steel flanges, Vacuum compotible sample puller rod, vacuum valves, Viton O-rings, Pirani/ Penning gouge and Mechanical pressure gauge.
Heated Length from 100mm to 1000mm.
♦ Capable of 1 o·mbor vacuum in a clean empty work tube.
♦ High vacuum station consists tvrbo molecular pump/Rotary vane pump with related vacuum fittings.
♦ Mass flow gas control station consists multiple Moss flow controllers, Gas mixing system and related pipe fittings.
♦ Compact design for minimum space requirement.
♦ Rugged and durable Construction.
♦ Outer casing is mode up thick mild steel with duly powder coated or thick buffed stainless steel, gives long service life with extremely resistant.
♦ Multi-layer insulation with vacuum formed ceramic fibre or refractory bricks with low thermal mass.
♦ Furnace design with powerful heating elements i.e. FeCrAI and SiC in all sides of the work tube providing fast heating rate.
♦ Fast heat up and cool down rates.
♦ Temperature uniformity +/ - 5°C.
♦ Temperature control with PIO controllers .
♦ Power control with solid stole relays or Thyristor units for very precise temperature Control, wear-free and noiseless.
♦ High mechanical durability, short heating cycle and low power consumption.
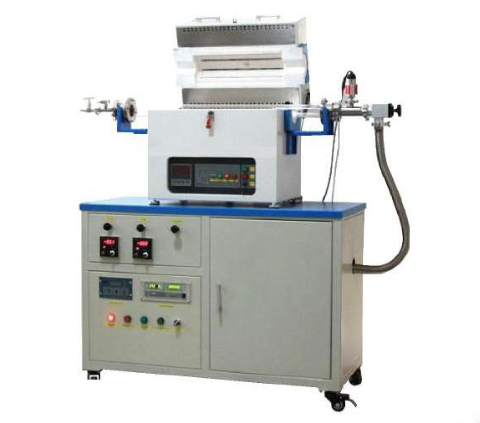
Options
♦ Multi-zone temperature control.
♦ Touchscreen temperature controller.
♦ Over Temperature limiter.
♦ Door flanges with hinges.
♦ Water cooled flanges with chiller.
♦ Digital/ Analog flow meters.
♦ Port for additional thermo couple on the flange.
♦ Process observation window on flange.
♦ Buzzer, Digital timer, Emergency shut down.
♦ Data Recorder.
♦ RS232/RS485/USB interface.
♦ Calibration of temperature measurement systems.
♦ Data Acquisition System (DAS) through software.
♦ UPS Systems.
♦ Customization as per user requirement.
♦ Caster wheels with brakes .
Applications
CVD Furnace is designed for R&D labs, Educational institutions, Medicine and Industry, ,
Aerospace industry, Semiconductor industry, Chemical Industries, Biomedical Industry, Pharma
Industry, gloss Industry, Thermal Process Technology, Advanced Materials for following
Applications-
Chemical analysis, Grophene ,Optical Fibre, Composition, Deposition, Diffusion,Cooling, ,br>
Degassing,Sintering, Catalyst research, Carbon nanotechnology process etc.
MUFFLE CUM TUBE FURNACE
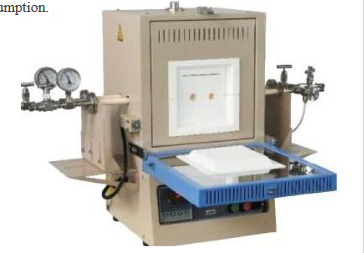
Features
♦ Maximum operating temperature range up to 1800°C.
♦ User can be uses both ways either Muffle or Tube furnace.
♦ Dimensions from 1 litre up to 27 litres.
♦ Compact design for minimum space requirement.
♦ Rugged and durable Construction.
♦ Outer cosing is mode up thick mild steel with duly powder cooled or thick buffed stainless steel, gives long service life with extremely resistant.
♦ Multi-layer insulation with vacuum formed ceramic fibre or refractory bricks with low thermal mass.
♦ Parallel guided swing aside door design.
♦ Half End Open Alumina/Quartz/Metal tube with two fibre plugs included.
♦ Inner diameter of the tube from 20mm to 150mm.
♦ Heated length from 100mm to 300mm.
♦ Furnace design with powerful heating elements i.e. FeCrAI, SiC and MoSi2 in bath sides providing fast heating rate.
♦ Fast heat up and cool down rates.
♦ Temperature uniformity +/- 5°C.
♦ Temperature control with PID controllers .
♦ Power control with solid state relays or thyristor units for very precise temperature Control, wear-free and noise less .
♦ High mechanical durability, short heating cycle and low power consumption.
Options
♦ Over Temperature/Over Current Limiter.
♦ Touchscreen temperature controller.
♦ Vacuum pump with fittings.
♦ Gas and Vacuum Compatible Flanges, Water cooled flanges with chiller.
♦ Door flanges with hinges.
♦ Gas mixing system.
♦ Digital/Analog flow meters.
♦ Port for additional thermo couple on the flange.
♦ Process observation window on flange.
♦ Buzzer, Digital timer, Emergency shutdown.
♦ Data Recorder.
♦ RS232/RS485/USB interface.
♦ Calibration of temperature measurement systems.
♦ Table/Stand for supporting the systems.
♦ Data Acquisition System (DAS) through software.
♦ UPS Systems.
♦ Customisation as per user requirement.
♦ Caster wheels with brakes.
♦ Door safety switch
Applications
Muffle Cum Tube Furnace is designed for R&D labs, Educational institutions, Medicine and Industry,
Chemical Industries, Plastic Industry, Moulding Industry, Gloss Industry, Rubber Industry,
Ceramics Industry, Biomedical Industry, Point Industry, Textile Materials, Pharma Industry,
Dental lobs, Thermal Process Technology, Advanced Materials for following applications,
Testing,
Purification, Coating, Analysing, Ashing ,Drying Sintering, Annealing, Brozing, Calcinot ion,
Degassing, Melting, Tempering, Hardening, Testing of fuel cells, Catalyst research, Inorganic
and Organic purification, Dental Porcelain, and Crystalizing etc.
VACCUM FURNACE
Features
♦ Maximum operating temperature range up to 1800°C.
♦ Depending upon application, a tube furnace con be designed in many sizes and shapes; most commonly these units ore classified
as Horizontal Tube Furnace, Vertical Tube Furnace, Horizontal split Tube Furnace, Vertical split Tube Furnace, Muffle Cum Tube Furnace.
♦ Capable of 1o·' mbor vacuum in a clean empty work tube .
♦ Compact design for minimum space requirement.
♦ Rugged and durable Construction.
♦ Outer cosing is mode up thick mild steel with duly powder coated or thick buffed stainless steel, gives long service life with extremely resistant.
♦ Multi-layer insulation with vacuum formed ceramic fibre or refractory bricks with low thermal mass.
♦ High Purity Alumina/Quartz/ Metal tube with two fibre plugs included .
♦ Inner diameter of the tube from 20mm to 150mm.
♦ Heated Length from 100 mm to 1000mm.
♦ Furnace design with powerful heating elements i.e . FeCrAI, SiC and MoSi2 in all sides of the work tube providing fast heating rate.
Vacuum provide by turbo molecular pump/ Rotary vane pump with pironi/penning gouges and related fittings.
♦ Work tube connects with the vacuum system via stainless steel below pipe.
♦ Access lo the work tube con be removable via stainless steel vacuum flanges.
♦ Radiation shields at both end of the work tube to maintain uniformity without reducing pump speed.
♦ Fast heat up and cool down rates.
♦ Temperature uniformity +/ - 5°C.
♦ Temperature control with PID controllers.
♦ Power control with solid state relays or Thyristor units for very precise temperature Control, wear-free and noiseless.
♦ High mechanical durability, short heating cycle and low power consumption.
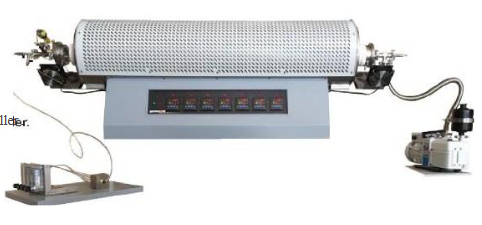
Options
♦ Multi-zone temperature control
♦ Touchscreen temperature controller.
♦ Over Temperature Limiter.
♦ Vacuum pump with fittings
♦ Gas and Vacuum Compatible Flanges, Water cooled flanges with chiller.
♦ Door flanges with hinges.
♦ Gas mixing system.
♦ Vacuum pump with fittings.
♦ Port for additional thermo couple on the flange.
♦ Process observation window on flange.
♦ Buzzer, Digital timer, Emergency shutdown.
♦ Data Recorder .
♦ RS232 / RS485/ USB interface.
♦ Calibration of temperature measurement systems.
♦ Table/Stand for supporting the systems.
♦ Data Acquisition System (DAS) through software.
♦ UPS Systems.
♦ Customisation as per user requirement.
♦ Caster wheels with brakes.
Applications
Vacuum Tube Furnace is designed for R&D labs, Educationa l
institutions, Medicine and Industry, Chemical Industries, Biomedical
Industry, Pharma Industry,Thermal Process Technology, Advanced
Materials for following applications- Chemical analysis, Physical
decomposition , sublimation, Purification, Coating, Drying,
Hardening or Ageing of samples, Brazing, Colcinotion, Degassing,
Sintering, Tempering, Testing of fuel cells, Catalyst research,
Inorganic and Organic purification, Coating etc.
CRYSTAL GROWTH FURNACE
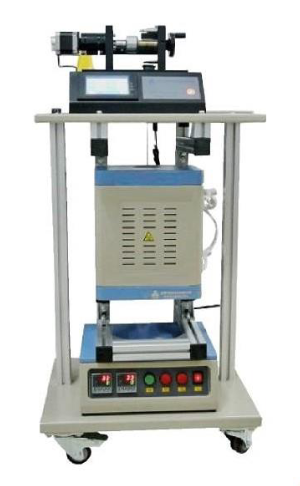
Features
♦ Maximum operating temperature range upto 1500 °C.
♦ The Bridgmon method uses that sample moves slowly through a temperature gradient in vertical tubular furnace.
♦ The melted material moves through a decreasing temperature gradient and form s a single crystal.
♦ Compact design for minimum space requirement.
♦ Rugged and durable Construction.
♦ Outer cosing is made up thick mild steel with duly powder cooled or thick buffed stainless steel, gives long service life with extremely resistant.
♦ Multi layer insulation with vacuum formed ceramic fibre or refractory bricks with low thermal mass.
♦ Furnace design with powerful healing elements i.e. FeCr AI SiC in all sides of the work lube providing fast heating role.
♦ In this system tube furnace mounted on stand with the pulling device.
♦ Precisely defined and controlled pulling speed.
♦ The movement of the sample can be fast for loading and unloading or with a user defined speed for crystal growth.
♦ Pooling device moves the sample with on adjustable speed toward the lower temperature.
♦ Alumina/Quartz/Metal ! ceramic tube surrounds the sample.
♦ Inner diameter of the tube from 50mm to 100mm.
♦ Healed Length from 100mm lo 1000mm.
♦ fast heat up and cool down rates.
♦ Temperature uniformity + / - 5°C.
♦ Temperature control with PIO controllers.
♦ Power control with solid state relays or Thyristor units for very precise temperature Control, wear-free and noiseless.
♦ High mechanical durability, short healing cycle and low power consumption .
♦ Auto and manual both operations possible with servo molar and driver.
Options
♦ Multi-zone temperature control .
♦ Touchscreen temperature controller.
♦ Over Temperature/Over Current Limiter.
♦ Gas and Vacuum Compatible Flanges, Water cooled flanges with chiller.
♦ Gas and Vacuum control accessories.
♦ Port for additional thermo couple on the flange.
♦ Buzzer, Digital timer, Emergency shutdown.
♦ Data Recorder.
♦ RS232/RS485/USB interface.
♦ Calibration of temperature measurement systems.
♦ Table/Stand for supporting the systems.
♦ Data Acquisition System (DAS) through software.
♦ UPS Systems.
♦ Customization as per user requirement.
♦ Caster wheels with brakes.
Applications
Bridgman type Furnace is designed for R&D labs, Medicine and lndustry, Pharma Industry,
Thermal Process Technology, Advanced Materials for following applications-
For crystal growth process.
ROCKING FURNACE
Features
♦ Maximum opemting temperature range up to 1300°C
♦ Designed for heating or melting to get more uniform reaction.
♦ The Rocking stage can set rocking frequency and time for automatically running.
♦ Compact design for minimum space requirement.
♦ Rugged and durable construction.
♦ Outer cosing is made up thick mild steel with duly powder coated or thick buffed stainless steel, gives long service life with extremely resistant.
♦ Multi layer insulation with vacuum formed ceramic fibre or refractory bricks with low thermal mass.
♦ Alumino/Quartz/Metal tube with two fibre plugs included .
♦ Inner diameter of the tube from 20mm to 100mm.
♦ Heated Length from 100mm to 500mm.
♦ Furnace design with powerful heating elements i.e. FeCrAI, in all sides of the work tube providing fast heating rote. Motorised, vibration free rocking operation.
♦ Adjustable speed up to 50RPM.
♦ Fast heat up and cool down rates.
♦ Temperature uniformity +/ - 5°C.
♦ Temperature control with PIO controllers .
♦ Power control with solid state relays or Thyristor units for very precise temperature Control, wear-free and noiseless.
♦ High mechanical durability, short heating cycle and low power consumption.
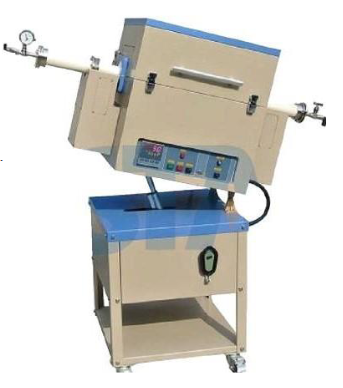
Options
♦ Multi-zone temperature control.
♦ Touch screen temperature controller.
♦ Over Temperature/Over Current Limiter.
♦ Vacuum pump with fittings.
♦ Gas and Vacuum Compatible Flanges, Water cooled flanges with chiller.
♦ Door flanges with hinges.
♦ Gas and Vacuum control accessories.
♦ Gas mixing system.
♦ Digital/Analog flow meters.
♦ Port for additional thermo couple on the flange.
♦ Process observation window on flange.
♦ Buzzer, Digital timer, Emergency shutdown.
♦ Data Recorder.
♦ RS232/RS485 /USB interface.
♦ Calibration of temperature measurement systems.
♦ Table/Stand for supporting the systems.
♦ Data Acquisition System (DAS) through software.
♦ UPS Systems.
♦ Customization as per user requirement.
♦ Caster wheels with brakes.
Applications
Rocking Furnace is designed far R&D labs, Educational institutions, Medicine and Industry,
Chemical Industries, Biomedical Industry, Pharma Industry, Thermal Process Technology,
Advanced Materials for following applications-
Mixturing, Purification, Cooling, Drying, Degassing, Sintering, Tempering,
Catalyst research, Inorganic and Organic purification, Coating etc.
RAISING HEARTH FURNACE
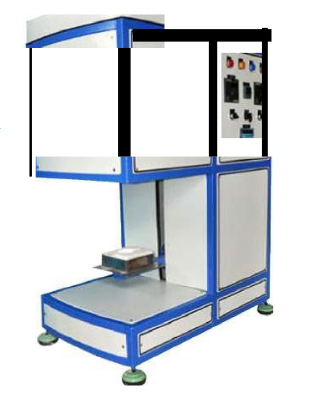
Features
♦ Maximum operating temperature range up to 1800°C
♦ Dimensions from 1 up to 64 Iitres.
♦ Compact design far minimum space requirement.
♦ Rugged and durable Construction.
♦ Outer casing is made up thick mild steel with duly powder coated or thick buffed stainless steel, gives long service life with extremely resistant.
♦ Multi layer insulation with vacuum formed ceramic fibre or refractory bricks with low thermal mass.
♦ Reliable vibration free bottom lifting with electro-mechanical movement
Prepared to carry heavy charge weight.
♦ Hot raising by hydraulic.
♦ Furnace design with powerful heating elements i.e. FeCrAI, SiC and MoSi2 installed in four walls of the chamber.providing fast heating rate and excellent temperature uniformity.
♦ Fast heat up and cool down rates.
♦ Temperature uniformity + / - 5°C.
♦ Temperature control with PIO controllers.
♦ Power control with solid state relays or Thyristor units.for very precise temperature Control, wear-free and noiseless.
♦ High mechanical durability , short healing cycle and low power consumption.
Options
♦ Over Temperature/Over Current Limiter.
♦ Touchscreen temperature controller.
♦ Port for additional thermo couple on top or rear wall of the furnace.
♦ Buzzer, Digital timer, Emergency shutdown.
♦ Data Recorder:
♦ RS232/RS485/USB interface.
♦ Calibration of temperature measurement systems
♦ Table/Stand for supporting the systems.
♦ Data Acquisition System (DAS) through software.
♦ UPS Systems.
♦ Customization as per user requirement.
♦ Caster wheels with brakes.
♦ Door safety switch.
Applications
Raising Hearth Furnace is designed for R&D labs,
Educational institutions, Medicine and Industry, Thermal Process Technology,
Dental Labs, Advanced Materials for following applications-
Drying, Hardening, Annealing, Brazing, Sintering,
Research, Heat treatment, Dental crowns and frameworks etc.
TUBE FURNACE
Features
♦ Maximum operating temperature range up to 1800°C.
♦ Available in, Horizontal operation, Vertical operation, universal operation.
♦ Compact design for minimum space requirement.
♦ Rugged and durable Construction.
♦ Outer casing is made up thick mild steel with duly powder coated or thick buffed stainless steel, gives long service life with extremely resistant.
♦ Multi layer insulation with vacuum formed ceramic fibre or refractory bricks with low thermal mass.
♦ Alumina /Quartz/Metal tube with two fibre plugs included.
♦ Inner diameter of the tube from 20mm to 150mm.
♦ Heated Length from 100mm to 1000mm.
♦ Furnace design with powerful heating elements i.e. FeCrAI, SiC and MoSi2 in all sides of the work tube providing fast heating rate.
♦ Fast heat up and cool down rates.
♦ Temperature uniformity + / - 5°C.
♦ Temperature control with PIO controllers.
♦ Power control with solid state relays or Thyristor units for very precise temperature Control, wear-free and noiseless.
♦ High mechanical durability, short heating cycle and low power consumption.
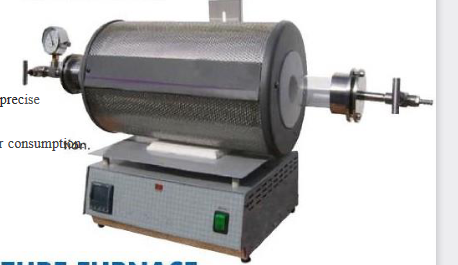
Options
♦ Multi-zone temperature control.
♦ Touchscreen temperature controller.
♦ Over Temperature Limiter.
♦ Vacuum pump with fittings.
♦ Gas and Vacuum Compatible Flanges, Water cooled flanges with chiller,
♦ Door flanges with hinges.
♦ Gas mixing system.
♦ Digital/Analog flow meters.
♦ Port for additional thermo couple on the flange.
♦ Process observation window on flange.
♦ Buzzer, Digital timer, Emergency shutdown.
♦ Data Recorder.
♦ RS232/RS485/USB interface.
♦ Calibration of temperature measurement systems.
♦ Table/Stand for supporting the systems.
♦ Data Acquisition System (DAS) through software.
♦ UPS Systems.
♦ Customization as per user requirement.
Applications
Tube Furnace is designed for R&D labs, Educational institutions, Medicine and Industry,
Chemical Industries, Ceramics Industry Biomedical Industry, Pharma Industry,
Thermal Process Technology, Advanced Materials for following applications-
Purification, Coating, Drying, Hardening or Ageing of samples, Annealing, Brazing,
Calcination, Degassing, Sintering, Tempering, Thermo couple calibration, Testing of fuel cells,
Catalyst research, Inorganic and Organic purification, Coating etc.